长期以来,钢铁工业因其大型复杂流程工业,全流程各工序均为“黑箱”。为打破这一“黑箱”,江苏省镔鑫钢铁集团建成国内钢铁行业首家基于原厂改造的全流程智能制造工厂,与今年4月起施行的《江苏省数据条例》中提出的“支持工业企业实施智能化改造、数字化转型和网络化联接”不谋而合。通过打造基于工业互联网平台的动态智能系统,全流程数字化支撑起这家智能制造工厂外部经营与内部管控的联动与持续再提升。
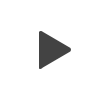
走进镔鑫钢铁的智控大厅,电子屏上实时跳动着从厂区内采集的各种数据,将实体工厂搬上屏幕,打造出贯穿钢铁生产全流程的“虚拟工厂”。通俗的说,这里的一项重要功能就是“把数据从黑箱里拿出来”。
镔鑫钢铁信息部部长黄江云介绍,全流程智能工厂以工业互联网平台为底座,结合大数据、云计算、边缘计算等先进技术,平台目前可集成35万个现场采集设备点位的业务数据,纵向打通数据传送链路,横向贯通各生产工序。截至目前,已累计产生、处理数据240亿条。
钢铁行业70%的成本在于高炉。在传统的高炉生产过程中,会有大量参数波动,同时在冶炼过程中也会产生一定的化学成分,需要靠老师傅的经验进行判断。而如今通过将采集到的数据深度应用于模型算法之中,实现了“精准号脉”。此外,管控一体化平台、产销一体化系统通过分析大量数据,有效减少成品库存,使全局经济指标明显提升。
对于数据的应用,也使得提高了生产安全性。通过将危险点位操作台等生产现场的点位全部部署到智控大厅,现场的数据信息在平台实时呈现。通过视觉监控+AI风险识别预警,以及操作辅助决策+HMI(人机界面),在大厅里就可以对远在几公里外的现场设备进行远程操作。如今,1个员工就可以控制之前15个同岗位、同工序的一些长线操作,实现生产大规模远距离智能集控。
正是依靠一系列数字化改造举措,今年以来,镔鑫钢铁每吨钢生产成本比2年前下降104元,人均生产率提高30%;炼铁厂结合智能应用的18个工业模型,使用率和准确率提升;原料加工车间年度降本指标41%,并通过外销铸铁块及铁水提升效益3000万元;炼钢厂实现工序成本HRB钢种系列降低约110元/t,钢铁料消耗降幅2.38kg/t。
黄江云表示,镔鑫钢铁始终致力于通过数字化破解钢铁行业的“黑箱”困局,通过以‘智’赋能,基于智慧工厂项目,在产销、铁区、钢轧和管控等方面实现四个‘一体化’,在组织能效、质量稳定、指标提升和成本攻关等方面取得显著成效。
【企业感受】
“我们注意到,《江苏省数据条例》提出,发挥制造业数据资源优势,提高制造业。”黄江云表示,智能制造是一个不断发展和完善的过程。集团将以《条例》为指引,期待与各方携手共进,实现传统制造业的“华丽转身”,共同推动钢铁工业“新质生产力”实践落地。
【法规链接】
《江苏省数据条例》第五十四条
县级以上地方人民政府、工业和信息化等有关部门应当推动数据在制造业等工业领域的发展应用,支持工业企业实施智能化改造、数字化转型和网络化联接,推进智能车间、智能工厂建设,提升工业互联网应用水平;发挥制造业数据资源优势,提高制造业数据治理能力和供给水平,推动构建制造业等工业领域基础数据库和与先进制造业集群匹配的特色高价值数据集,为先进制造业发展提供高质量数据支撑。